K-Phase is an adjustment we can make in the motor controller, that describes the profile of a specific motor, in the controller – more specifically the phase angle adjustment depending on the speed. Compared with a car engine, K-Phase is like adjusting the ignition point depending on the speed, ensuring the highest possible efficiency and power at all speeds!
In MIS/SMC firmware prior to 6.08, the K-Phase value was a single value, setting 1 graph for 1 motor. This was simple, and would work in general, but not always for high velocity and/or at a wide range of supply voltages.
In MIS/SMC firmware 6.08, we introduced K-Phase as 4 values with greatly improved performance. This is standard in all closed-loop ServoStep™ motors.
The new K-Phase parameters ensures better performance for all motors.
With optimized K-Phase values, even huge motors like the 12Nm MIS343 can run 3000 RPM with just a 24 VDC supply voltage!
Optimizing the K-Phase for your specific application can improve the performance massively.
When tested on MIS176S in a no-load test, the new default K-Phase values resulted in up to 81% lower running torque and 50% lower current consumption!
Adjusting the K-Phase parameters for the specific motor and application, using the automated calibration, resulted in up to additional 43% lower running torque and 38% lower current consumption.
ServoStep™ is a world leading servo motor, based on a stepper motor with closed-loop servo control. This gives the high torque density and easy control of a stepper motor, combined with the performance and dynamics of a servo motor.
Below are some highlighted benefits from the JVL ServoStep™:
- Always in control – no stalling and no steps lost
- Real servo performance – high speed, high dynamics and high possible duty cycle
- High positioning accuracy – 409600 cnts/rev with complete stand-still
- High inertia tolerance – can often be used directly without a gear
- Extreme torque density – up-to 25 Nm without gear
- High efficiency – green production and lower heat
Which factors influences the K-Phase
The K-Phase values set in the motor is depending on many criteria:
- Supply voltage level P+ - High impact on performance
- Motor size - High impact on performance
- Speed of the motor - Low impact on performance
- Running current - Impact on performance only in case of resonance
- Possibly also temperature - Low impact on performance
- Individual motor - Low impact on performance
K-Phase calibration
The K-Phase can be automatically calibrated to your application.
Specific calibration is rarely needed, but in special cases where you find issues with the motor performance, typically if you use a very low supply voltage like 12VDC, use very high speed like +2000 RPM, or if you use some of the biggest motors like MIS341 and above, a specific calibration or specific K-Phase values can be a good solution.
The calibration requires that the shaft is free, and the motor has the same supply voltage, current setting and best also temperature as used in your application.
- Set the speed to MAX e.g. 3000 RPM – if your application never exceeds e.g. 1500 RPM, you can try with this value as well.
- Set the current to MAX (unless there is resonance in the body, in that case turn in down a little).
- Use the same supply voltage as in the actual application where the motor will be used.
- In command register 24, execute command 999 and afterwards execute command 902
- When Register 51(P2) is set to 100 the calibration is done.
- Execute command 999 and afterwards command 720 to save the calibration, and power cycle the motor.
- If the motor still does not perform well at the desired speed, you can try to change the speed in MAX Velocity and run the calibration again.
To undo and
go back to the default setup:
- In command register 24, execute
command 999 and afterwards execute command 721 to load default K-phase
parameters stored in the firmware.
- Execute
command 999 and afterwards command 720 to save the calibration, and power
cycle the motor.
K-Phase behind the scenes
The K-Phase values must fit the characteristics of the specific motor. To find the values, we have internally recorded a high-resolution graph for each MIS motor at 12, 24, 48 and 72VDC.
This graph tells where to set the points of medium and high-speed velocity and the equivalent off set values.
K-Phase is set in registers 327, 328, 329 and 330.
These values combined sets a medium and high-speed velocity, and then an offset for each.
Currently the K-Phase values are set to fit all voltage levels, but since the supply voltage level has a huge impact on the motor characteristics, we are working on a system to have independent values for different voltage levels.
But in the meantime, we have found good values for all motors, that ensures the best overall performance.
It is possible to do a specific calibration for your specific application, with specific supply voltage and speed. This can be done as preconfigured values we select, or you can do a calibration locally.
The K-Phase characteristics can look like below, where MIS232S/Q is used as an example.
The blue area is where the motor is most efficient, where the least running torque is used, and the yellow area is where the motor is least efficient, and in the extreme case cannot rotate at the desired speed, because the running torque is at 100% - Please remember that the JVL closed-loop ServoStep™ motors will not stall, they will simply not reach the full speed in this case.
The values of below graphs are:
327: 6500
328: 548485
329: 102626
330: 1381
|

|
Above K-Phase values will give a general good performance, but if you know that you use e.g., 12VDC supply voltage, you might want to consider below values:
327: 5290
328: 874143
329: 106936
330: 1935
|
Standard:
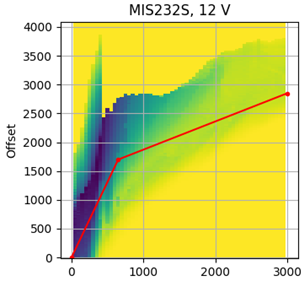
|
Optimized for 12VDC supply:
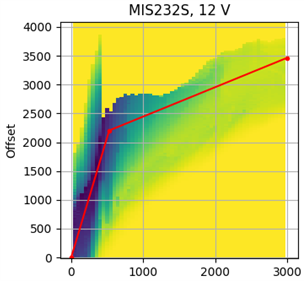
|
The values seem simple, but it will always require a complete test of the motor, to ensure the level of performance.
JVL can set up your motor for a specific value. This requires a customer specific part number.
Alternatively you can run the automated K-Phase calibration.